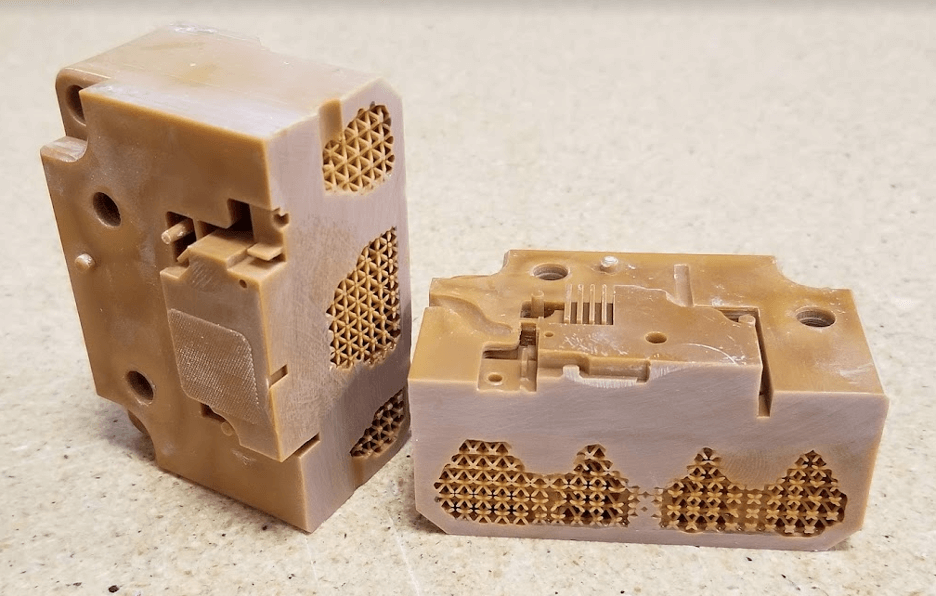
Akadeum Life Sciences, the global leader in buoyancy-based technology, has developed Buoyancy-Activated Cell Sorting (BACSTM) which is their patented approach to cell separation offering a new way to isolate the target of interest (cells, nucleic acids, proteins, etc) using buoyancy. During a new product development cycle, they needed to prototype a valve that could act as a seal while also spinning to isolate the target of interest. The valve is overmolded onto a rod that spins within the test tube.
They turned to Planet Innovation, a healthcare innovation and commercialization company, and Empire Group, a full-service product development and manufacturing company, for the design, development, and manufacturing. This case study discusses the design, prototyping, design iteration, and manufacturing of the valve.
It is widely known that prototyping in a fast, effective, and low-cost way is the key to de-risking projects that need to get to market quickly. A lesser-known advantage of leveraging 3D printed tooling is spending less capital on product development to rapidly test functional prototypes and manufacturability using engineered resins. This case study demonstrates how Planet Innovation leveraged 3D printed injection mold tools for prototyping to take advantage of those key points for their client.
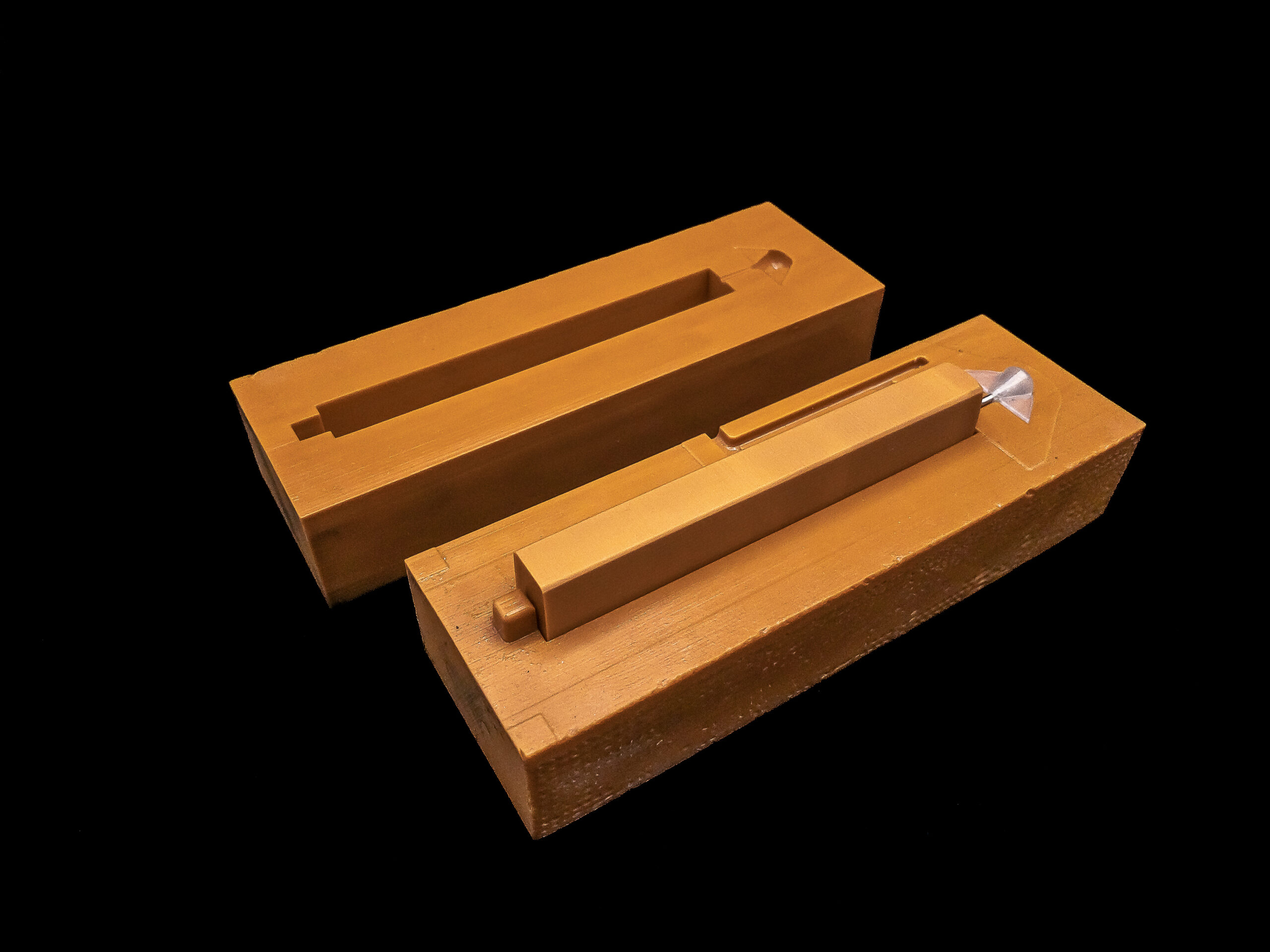