Next generation RF beamforming
Increase gain, widen field of view, and improve SWaP-C
Core Markets
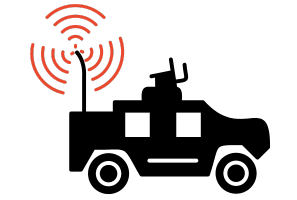
Supporting national security and the warfighter by enabling advanced 5G infrastructure, ISR, and radar technologies.
Wireless Infrastructure
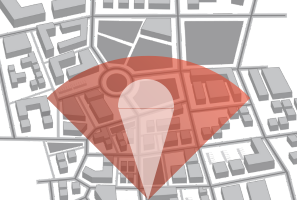
Improving mmWave base stations through enhanced directivity and field-of-view.
Satellite Communications
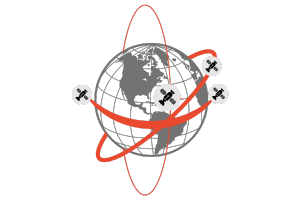
Enabling true multi-orbit and multi-band satellite communications.
Security
& Detection
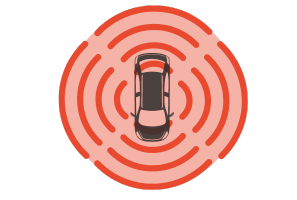
Improving performance of traditional sensors and radar through lensing.
Break free from design and manufacturing constraints with our advanced manufacturing, materials, and design expertise.
Whether you have a clear vision for your project or require assistance in identifying solutions, Fortify stands ready to provide you with the necessary tools to swiftly and efficiently tackle your most critical challenges.
Engage with Us
From solution identification to production, Fortify has the process and expertise to mature your application across it’s lifecycle
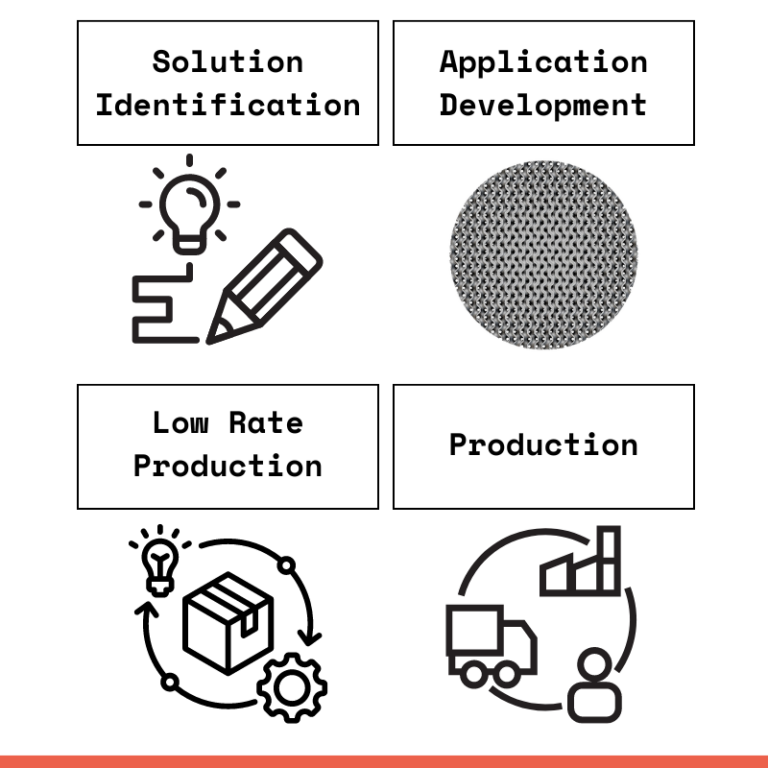
Our Technology is Trusted By
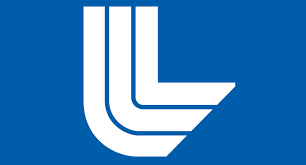
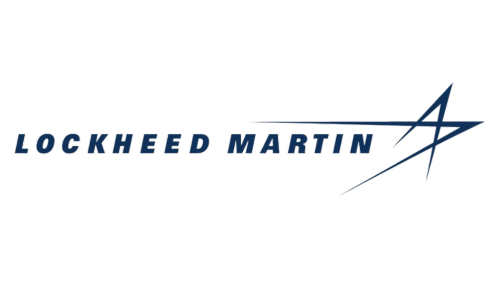
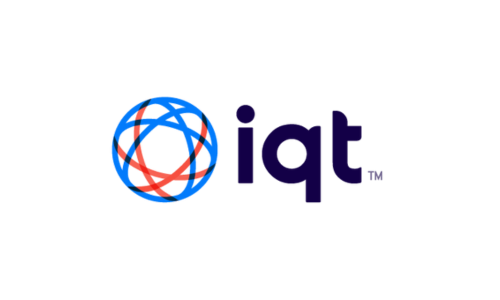
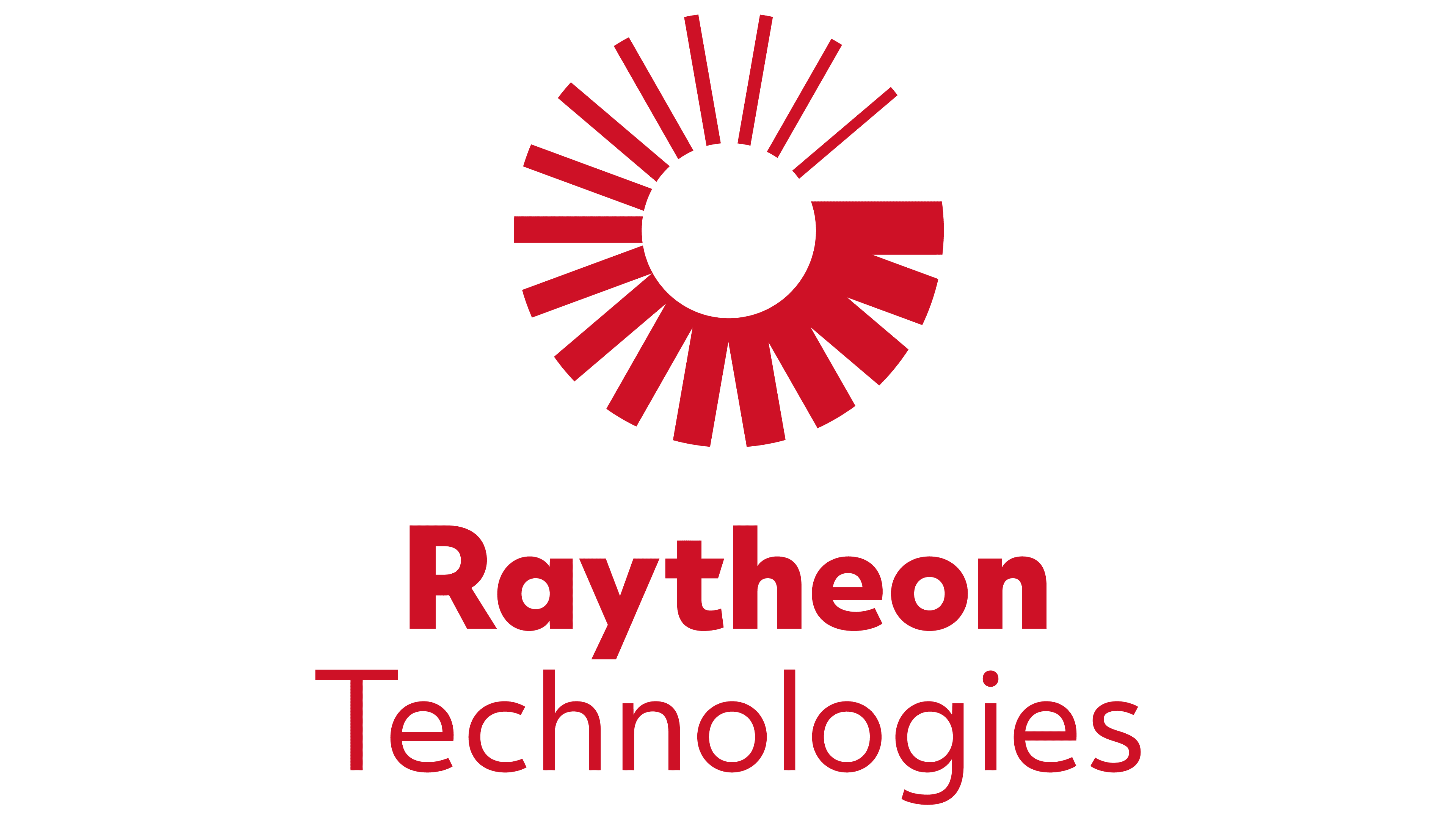
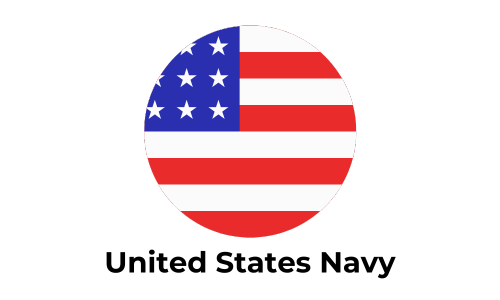
Resource Center
Search our online resource center for solutions to your application.
Includes White Papers, Case Studies, Guides, Articles, Data Sheets, and other literature. Search by application, industry, or keyword.
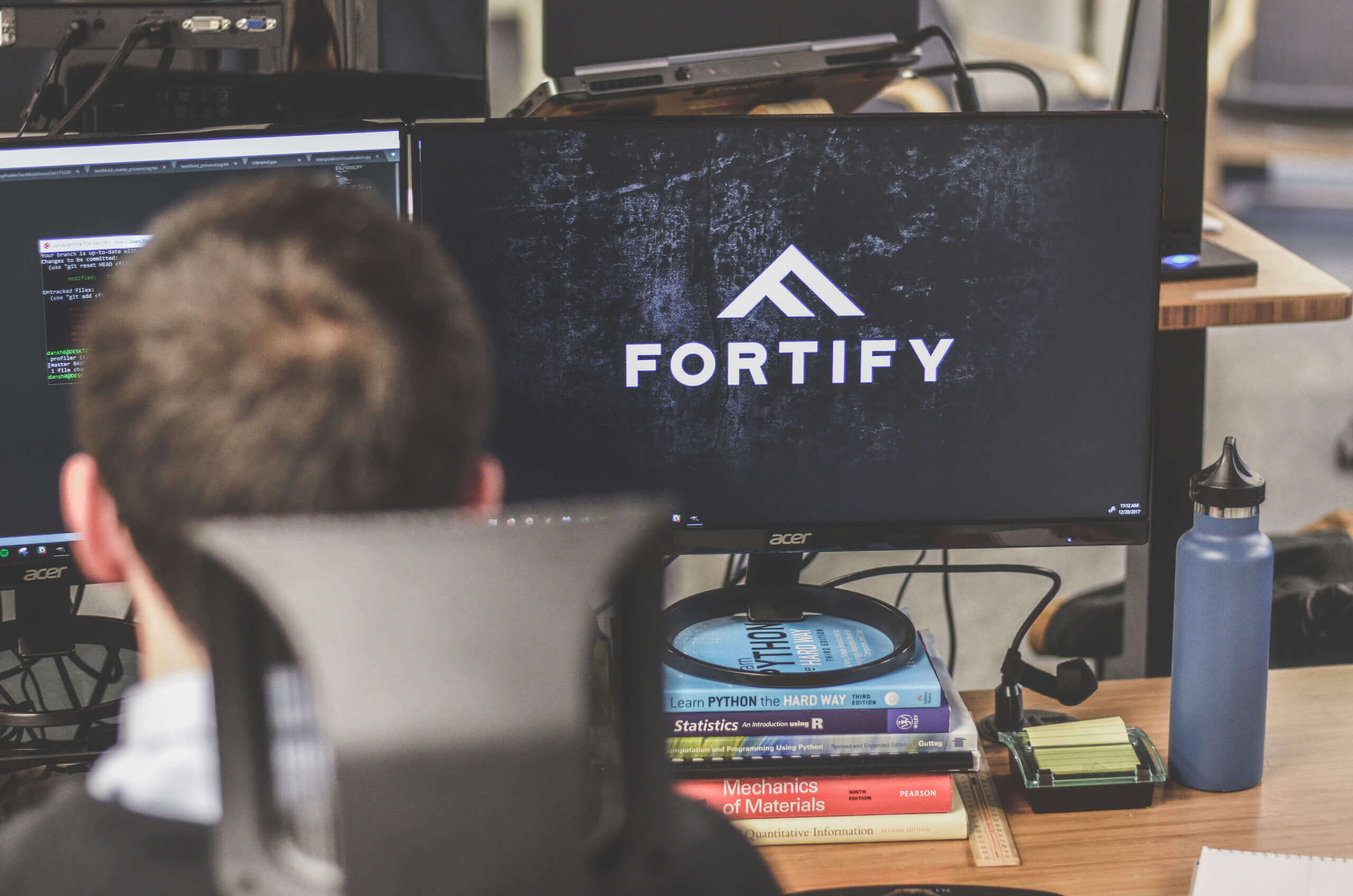