What is Fluxprint?
Imagine creating fully-optimized composite materials with the press of a button. Magnetic 3D printing, or Fluxprint, does just that. No complex fabrication, no sub-par materials. Just custom composites within hours.
Fluxprint is an additive manufacturing process that creates precisely-tailored composites such as carbon fiber. This method combines the benefits of 3D printing and composites. Composites are among the most advanced materials available. 3D printing is an incredibly fast, hands-off fabrication process that can form nearly any geometry. Fluxprint goes a step further by precisely tailoring composites voxel-by-voxel to create the ideal material for a project.
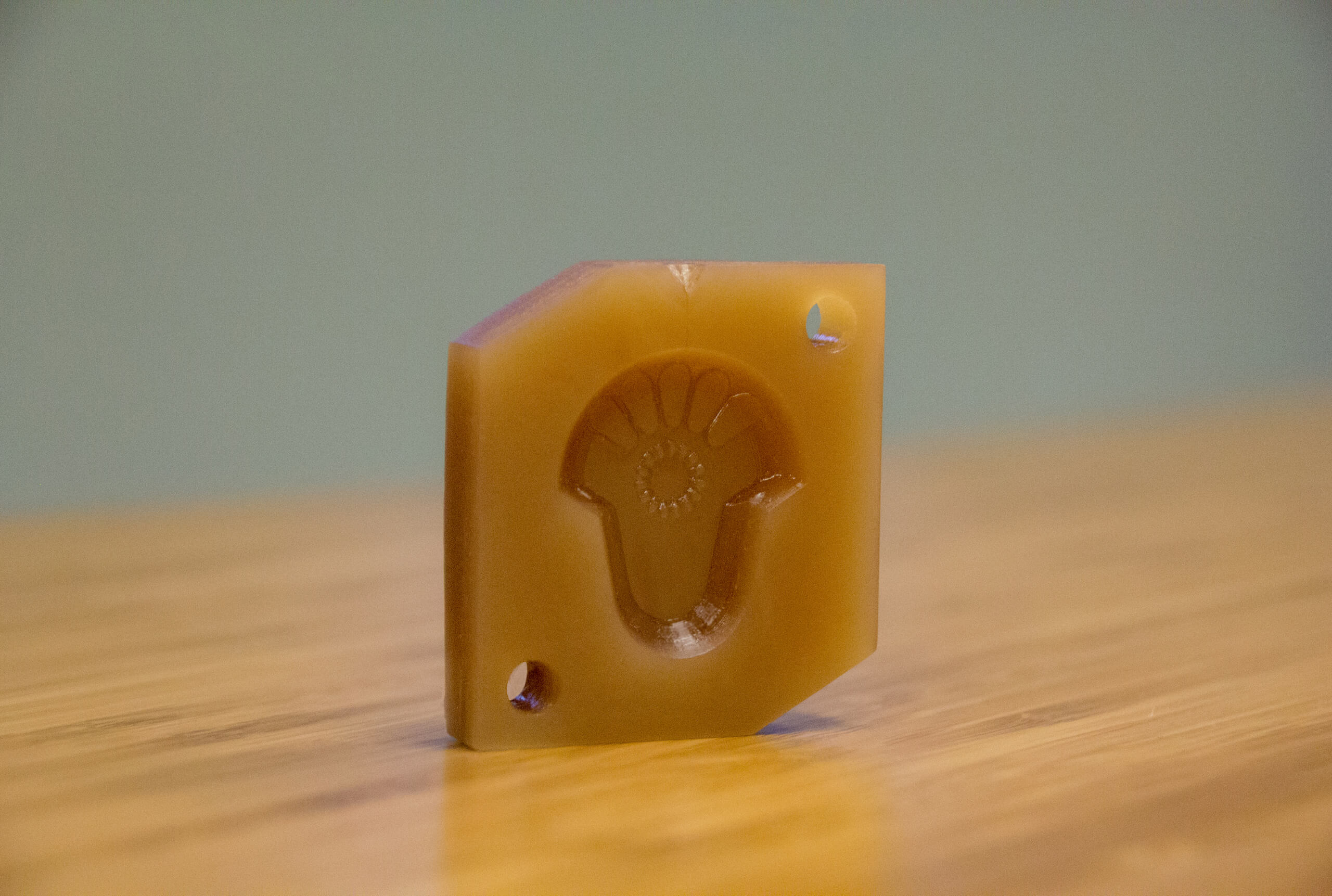
Fluxprint can produce durable parts in detailed geometries such as this injection mold.
The Purpose of Fluxprint
Fluxprint produces fully customized composite materials. Composites such as carbon fiber have incredible mechanical properties; carbon fiber outperforms steel, aluminum, and engineering plastics in most applications. If everything could be made of composites, they would be. But composites are a less common material because of their traditional lay-up fabrication process, which is time-consuming and expensive.
With Fluxprint, composites can not only be quickly and easily formed into any geometry but they can also be tailored precisely to meet the needs of the project. Strength, stiffness, weight, and other mechanical properties can be adjusted voxel by voxel. The result is functional printed parts for applications that could not otherwise be made with 3D printing.
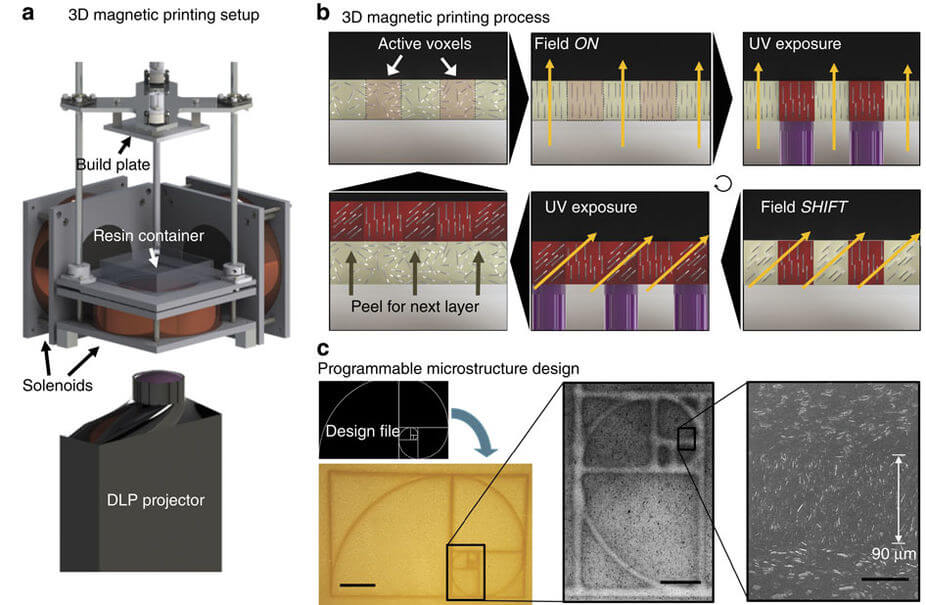
The Fluxprint process uses DLP 3D printing and magnets to create a fully-optimized, high-resolution object. Scale bar: (c) 2, 500, and 50 mm from left to right.
How Fluxprint Works
In Fluxprint,
(a) Electromagnets apply a precise magnetic field to a composite SLA resin.
(b) A digital light processing (DLP) projector selectively polymerizes the composite resin.
(c) Steps (a) and (b) are repeated multiple times within each layer to achieve different alignment directions.
(d) The build plate moves upwards to repeat steps (a)-(c) in a new layer.
(e) Steps (a)-(d) are repeated until a tightly-toleranced part has been produced with a composite microstructure that is optimized for its application.
Fluxprint can produce detailed reinforcement micro-architectures such as the Golden Ratio (above) that exhibits discrete reinforcement regions of 90 μm and lower.
Applications of Fluxprint
Fluxprint is a revolutionary fabrication method in the automotive industry, aerospace, and product design. In auto design, cars are stronger, lighter, and safer with guided stress cracking, all while saving time and money in fabrication. The same goes for aerospace, where it’s essential to optimize material properties for a safe, lightweight aircraft. Fluxprint also brings the benefits of composites to injection molding; composite injection mold tools can be made in days instead of months, and produce hundreds of accurate prototypes molded with end-use plastics. Across a range of industries, Fluxprint is replacing parts that were previously machined, cast, or molded with hands-off digital fabrication and optimized material properties.
Fluxprint is the Fluxprint process that fuels Digital Composite Manufacturing. With DCM, you can have fully-optimized composites in hand within hours. This manufacturing method opens up the benefits of 3D printing to high-performance parts. This means low cost, high speed, limitless geometries, and no machining required. DCM opens up new possibilities in materials, making fabrication faster and products better.